Pressure regulator
Pressure regulators are found in many common household and industrial applications. For example, pressure regulators in gas furnaces to regulate propane, in home heating furnaces to regulate natural gases, in medical and dental equipment to regulate oxygen and anesthetic gases, in pneumatic automation systems to regulate compressed air, in engines To regulate fuel and in fuel cells to regulate hydrogen. As this partial list shows, there are many applications for regulators, but in each of them, the pressure regulator provides the same function. Pressure regulators reduce a supply (or inlet) pressure to a lower outlet pressure and work to maintain this outlet pressure despite fluctuations in inlet pressure. Reducing inlet pressure to lower outlet pressure is a key feature of pressure regulators.
There are many factors to consider when choosing a pressure regulator. Important considerations include: operating pressure range for inlet and outlet, flow required, fluid (is it a gas, liquid, toxic or flammable?), expected operating temperature range, material selection for regulating components including seals and Wax as well as size and weight restrictions.
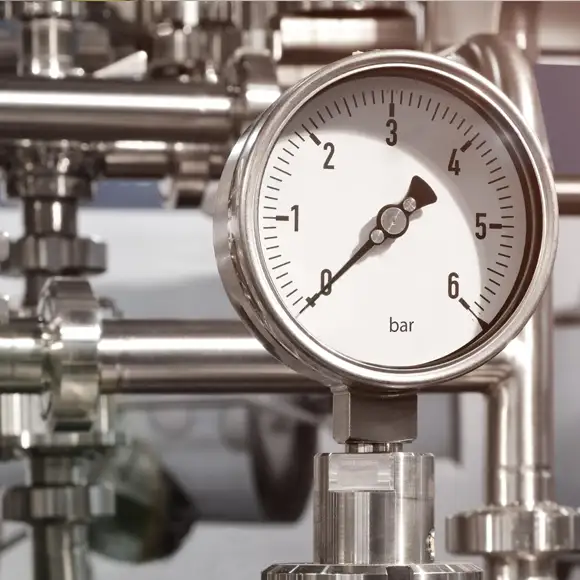
Materials used in pressure regulators
A wide range of materials are available to handle different fluids and operating environments. Common regulator components include brass, plastic, and aluminum. Various types of stainless steel (such as 303, 304 and 316) are also available. The springs used inside the regulator are usually made of music wire (carbon steel) or stainless steel.
Rice is suitable for most common applications and is usually affordable. Aluminum is often specified when weight is a concern. Plastics are considered when low cost is a primary consideration or disposal of items is required. Stainless steels are often chosen for use with corrosive fluids, use in corrosive environments, when fluid cleanliness is a concern, or when operating temperatures are high.
Equally important is the compatibility of the sealing material with the fluid and with the operating temperature range. Buna-n is a common sealant. Optional seals offered by some manufacturers include: fluorocarbon, EPDM, silicone, and perfluoroelastomer.
Single stage pressure regulator:
High pressure gas enters from the source through the inlet valve. The gas then enters the body through the regulator, which is controlled by the valve. In this case, the pressure increases, which pushes the diaphragm and closes the inlet valve connected to it, preventing any more gas from entering the regulator. A pressure gauge is installed on the outlet side. . The gas is drawn from the outlet side and the pressure inside the body is adjusted.
The diaphragms are pressurized and the valve opens, and more gas enters the source until the balance between the outlet pressure and the spring is established. Therefore, the output pressure in the spring force can be adjusted using a handle or adjustment knob. The outlet pressure and inlet pressure keep the diaphragm / POPPET in the closed state against the force of the SPRING.
If the source pressure drops, because the spring pressure has increased, it allows more gas and higher pressure to enter the outlet chamber to reach equilibrium pressure. Therefore, if the source pressure drops, the outlet pressure will increase. Supply output pressure is falling below supply pressure.
Two-stage pressure regulator:
It includes two single-stage regulators, which act to reduce pressure gradually in two stages instead of one. The first stage, which is predetermined, causes the supply gas pressure to decrease to an intermediate stage, and the gas under pressure passes to the second stage. The gas now emerges at the pressure (working pressure) determined by the setting pressure of the control knob attached to the diaphragm. The two-stage regulator has two safety valves, so that there is no explosion in case of any overpressure. The big problem with the single-stage regulator is the need for frequent torque adjustments.
If the source pressure drops, the output pressure increases, which requires torque adjustment. In the two-stage setting, there is automatic compensation for any drop in supply pressure. The single-stage regulator may be used with pipelines and cylinders. Two-stage is used with cylinder and manifold.
Function of pressure regulator:
The primary function of a pressure regulator is to match the gas flow through the regulator to the demand for gas, while the outlet pressure is constant.
If the load current decreases, then the regulator current must also decrease. If the load flow increases, then the flow regulator must increase the pressure in order to maintain pressure drop control due to the lack of gas in the system. A pressure regulator consists of a self-healing element, a loading element, and a metering element. Is:
• The loading element is the valve which can apply the necessary force to limit. Like GLOBE VALVE, BUTTERFLY VALVE, POPPET VALVE and…
• Measuring element functions to determine when the input current is equal to the output current. The aperture itself is often used as a measuring element; It can be used as a composite element.
In the single-stage regulator image, a force balance on the diaphragm is used to control a valve for pressure regulation. With the input pressure, the SPRING above the diaphragm pushes it down on the valve, to adjust the pressure. When the inlet pressure is introduced, the POPPET opens, allowing flow to reach the diaphragm and the pressure in the chamber increases, until the diaphragm is pressed upward against the spring, causing the flow of the POPPET to decrease. It stops further increase in pressure. By adjusting the top screw, the downward pressure on the diaphragm can be increased, thus requiring more pressure in the upper chamber to maintain balance.